Offline Filters have been used for decades to effectively control contamination and greatly improve reliability in lubricated machinery. In the world of maintenance and reliability, they are essential. Yet, myths abound about the use of Offline Filters. Some myths arise from general confusion about filtration. Others are simply half-truths or hearsay passed along and accepted as fact. This paper walks through 10 common myths that have been proven wrong – and uncovers a few surprising truths that can help take your reliability program to the next level.
Myth No. 1: I Have an Inline Filter – I Don’t Need an Offline Filter
80% of hydraulic and gear failures can be traced to excessive contamination. This occurs in spite of the fact that these machines come equipped with Inline Filters. Factory supplied filters are often chosen based on the lowest price – not upon their ability to maintain clean oil. An independent study at Tampere University of Technology in Finland showed that 10 leading brands of Inline Filters failed to live up to the filtration ratio printed on the product. Offline Filters make up for this deficit by providing fine filtration in a “kidney loop” process. This involves drawing oil from the bottom of the tank or reservoir and passing it through highly efficient filters to remove contaminants. Once clean, the system will stay clean when using Offiline Filters. Plus, they remove Water, Varnish and Acids that Inline Filters simply can’t.
NOTE: A gearbox came equipped with a highly rated Inline Filter from the factory. In just 3 months after start up and commissioning, the oil was at the condemning level and a complete gearbox replacement was under consideration. Instead, an Offline Filter was retrofitted and in just 10 days the oil was cleaned to better than new levels and the gearbox continues in service to this day (see Figures 1-2).
Myth No. 2: Offline Filters Will Remove Additives
Oil companies have developed sophisticated additive packages formulated to be fully dissolved in all types of lubricants, fluids and fuels. Just as sugar will dissolve in your favorite beverage, additives similarly dissolve into the oil. Experts agree that if the oil is formulated without solid additives, and if the additives are properly blended when new, these additives should not be filtered out even by Offline Filters with a fine filter element (1-3μm). TIP: Ask your filter supplier and oil supplier to provide documentation such as in-service oil analysis reports, written statements and filterability test results. They can provide assurance that the use of Offline Filters will not harm the additive package in your oil.Myth No. 3: Filter Carts and Offline Filters Are Equal
Just as not all oils are created equal, not all filters are created equal. Filter Carts cannot maintain oil cleanliness over time and varying application parameters. The only way to ensure cleanliness is to install a dedicated, full-time Offline Filter. Filter Carts have their place. However, modern Offline Filters provide fine filtration without taking up too much space. The cost of an Offline Filter is less than a Filter Cart. Significant savings are achieved over the service life because there is no labor involved in constantly moving and maintaining as is the case with Filter Carts. NOTE: The Sawtooth Curve (see Figure 3) illustrates the advantage of Offline Filters over Filter Carts. The difference between the two dotted lines is the difference in contamination levels maintained by Filter Carts (upper line) and continuous fine filtration with Offline Filters (lower line). The area in yellow represents contaminants left remaining by Filter Carts that will cause further damage. Figure 3: The Sawtooth Curve illustrates how Offline Filters outperform Filter Carts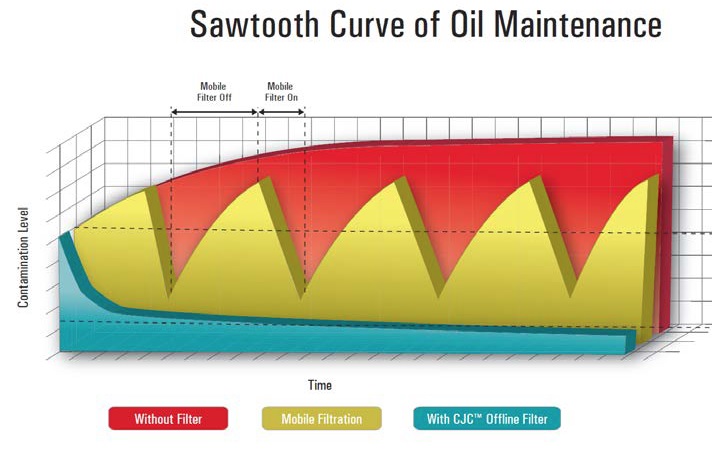
Myth No. 4: Bearings and Gears Don’t Need Offline Filters
Research going back nearly four decades dependably established that a bearing’s life can be extended by up to 7 times by using fine filtration to clean the oil. For instance, in 1979 a ground breaking study at London’s Imperial College by MacPherson proved that rolling element bearings in gearboxes can have a life extension factor of six by improving filtration from 40μm to 3μm (see Figure 4). Figure 4: The MacPherson Curve reveals that bearing life can be extended by as much as six times by changing from a 40 micron to a 3 micron Offline Filter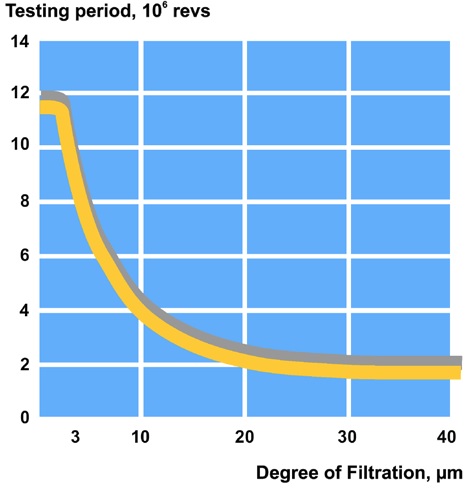
Myth No. 5: Offline Filters Are All the Same
Not all filters are created equal and not all Offline Filters are the same. Some filter suppliers take filter elements designed for Inline use and use them in an Offline system. But this may put your machine at risk. For instance, a 3μm surface-type Inline Filter can be installed Offline but what about Water removal, Varnish removal and Acid removal? What is the dirt-holding capacity? There are limits to how much dirt Inline Filters can remove. Would you prefer to change your filters monthly or yearly? Good quality Offline Filters should offer a depth type filter that removes all types of contaminants and a service life of 12 months or more.Myth No. 6: OEM’s Bear Responsibility for Selecting Offline Filters
The trend among many OEM’s and system designers is to provide a lower cost approach to contamination control. This is often justified in taking “cost out” of the final product. Cost out can mean cutting corners and, as a result, only the bare minimums are designed into the system such as Inline Filters and Breathers. To get the contamination control design right requires good cooperation and communication between OEM and End User. Nearly 80% of failures can be traced to contamination as the root cause. There can be confusion about who is responsible to address this risk: the OEM or the End User? Many failures occur during the warranty period when the machine is relatively new. Post warranty it becomes even more critical to ensure that there is an Offline Filter installed to get the longest possible service life. TIP: OEM’s and End Users should work together with filter suppliers to ensure that cleanliness requirements are maintained over the lifetime of the equipment. Develop a good working relationship between OEM’s and filter suppliers to get the right filters for the job and locate them properly. It will pay big dividends in the end.Myth No. 7: Offline Filters Cannot Clean High Viscosity Oils
Some filter suppliers claim that their products can be used with higher viscosity oils. The problem is that high flow requirements (i.e. oil cooler circuit) and low surface area of these filters does not allow sufficient space for high viscosity oils to pass through. The pressure drop gets too high, even if the oil is pre-heated. As a result, the filter runs in bypass. Inline Filters are best for viscosities < 200 cSt. Offline Filters on the other hand offer a much higher surface area and provide depth filtration (see Figure 5). They are designed to run at much lower flow rates. Therefore, they have been successfully installed in applications working with ISO VG 1000 cSt oil – and the oil is clean! ISO Codes of 16/14/11 or better are achieved. Figure 5: Offline Filters provide high surface area and depth filtration to handle high viscosity oils. Used Offline Filter (Left) compared to new Offline Filter (Right).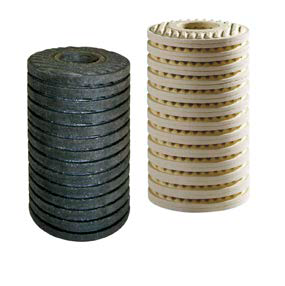
Myth No. 8: Not an Option for Clean Up After a Failure
After a failure, a complete drain, fill and flush is often carried out, but it comes at a cost. Offline Filters can dramatically cut the cost of restoring a system after a pump or motor failure. While a high amount of debris and contamination can be thrown into the system, an Offline Filter will handle it. The oil should be analyzed by an independent lab to ensure that it has not been degraded. If it is chemically in good shape, the dirty oil can be filtered and reused. Once the system has been circulated for a minimum of three times through the Offline Filter, the oil should be tested to ensure the system is clean. The Offline Filter should continue operating until cleanliness requirements have been met.Myth No. 9: Offline Filters Cannot Remove Varnish
Next to dirt and water, varnish is one of the bad pollutants in oil contamination. These so-called “soft” contaminants are really hard-core in terms of the damage done. Varnish works by means of stealth and it seems to appear out of nowhere, originating from the oil itself. The telltale signs of varnish contamination are high temperature, hot spots, water, aeration, high sub-micron particle counts, and low ant-oxidant levels. To capture varnish, you will need a net just like when capturing a criminal. However, this net has to be a very fine mesh with hooks to grab varnish particles. Cellulose commonly used in Offline Filters is ideal for capturing and detaining varnishing for good (see Figure 6). NOTE: Synthetic filter media such as Glass Fiber, commonly used with Inline Filters, cannot remove varnish. Use Offline Filters with cellulose depth media to remove varnish. Figure 6: Varnish captured and removed by an Offline Filter in 14 Days of operation on gas turbine lube oil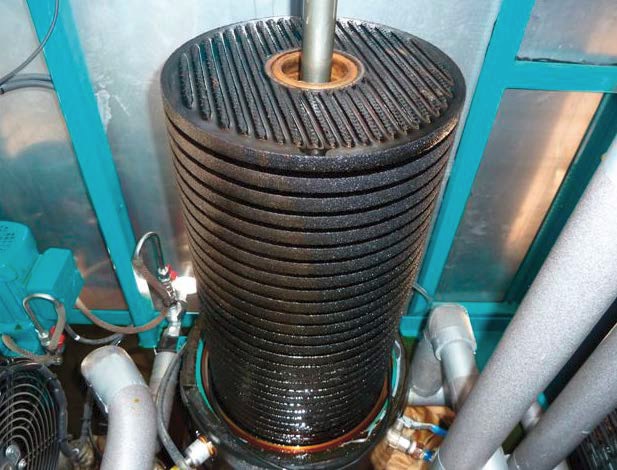
Myth No. 10: Special Oils or Additives Can Replace the Need for Offline Filters
Some oil and additive suppliers claim that their products can reduce wear, repair damaged components and even eliminate contamination. The problem is that wear and tear is inevitable. Eliminating contamination all together is impossible. It has been correctly stated that viscosity is the most important property of lubricants. However, of equal importance is the level of contamination. The vast majority of contaminants are tiny, less than 10μm. They are abrasive and hard. They swim around in the fluid blissfully grinding away at critical surfaces and seals. They arrive free of charge from the lubricant supplier. They are allowed in through poor maintenance. They are lonely little devils that “create” friends – one goes into your system and at least one more comes out as a result of wear processes taking place. Special Oils or Additives will not stop this. The only way to remove and control these contaminants is to install proper filtration. Offline Filters are the most effective choice for getting the oil clean and dry in your machine – and keeping it that way! Figure 7: Offline Filter installed on a Wind Turbine Gearbox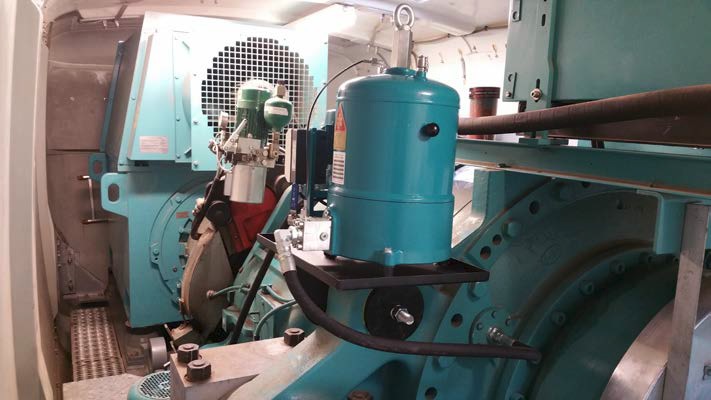